Photoblog: 5 Innovations we've made to Eco Brixs HQ to help tackle Uganda's Plastic Problem
- Andy Teale
- Oct 21, 2020
- 4 min read
The last 6 months have seen us make a number of changes to our main site in Masaka, Uganda. This has all been apart of our efforts to clean up Uganda's plastic waste whilst creating job opportunities for the local community, through the creation of our closed-loop system.
At the start of 2020, whilst our collection network of over 20 Community Recycling Centres around the region was bringing in 17 tonnes of plastic a month, we were still reliant on selling the plastic waste to the international market (to countries such as India) so it could be recycled. As we pay for every kilogram of plastic brought to us by the local community, this was key as it allowed us to generate income in order to keep funding the collection network, and therefore create income opportunities.
The plan has always been to create our own self-sufficient closed-loop system, where we sell products made from recycled waste in order to fund the network. However, to do this, we needed to make major changes to our HQ - to create a factory on-site in order to do this.
Thanks to our the generosity of our partners such as the Queen's Commonwealth Trust, the Alan & Nesta Foundation and Tearfund, and donations from individual supporters, we've taken another big step in doing this!
Our HQ is now looking very different from how it looked at the start of 2020...
The former Eco Brixs Site was mainly a hub to collect plastic from our network of Recycling Centres around the region, with a couple of basic structures in order to bail the plastic so it could be shipped internationally to be sold.
We purchased the machines which allow us to recycle plastic into products...
As the pandemic began to spread around the world, we purchased a small machine line, which included an Injection Machine and Product Mould so we could produce our first type of Eco-Products on a mass scale - COVID 19 Face Shields to protect people in Masaka, namely frontline workers at hospitals and local clinics.
Then, later in the year, we then purchased a larger machine line that would allow us to make a wider variety of items from recycled plastic...
The new Shredder Machine and Extruder allows us to create even more Eco-Products! To date, we've been able to experiment with Lumbar posts which can be used to create fencing and furniture, as well as turning plastic into fibre, allowing us to make clothing items such as the cap pictured above!
We up-cycled a shipping container to house the new machine lines...
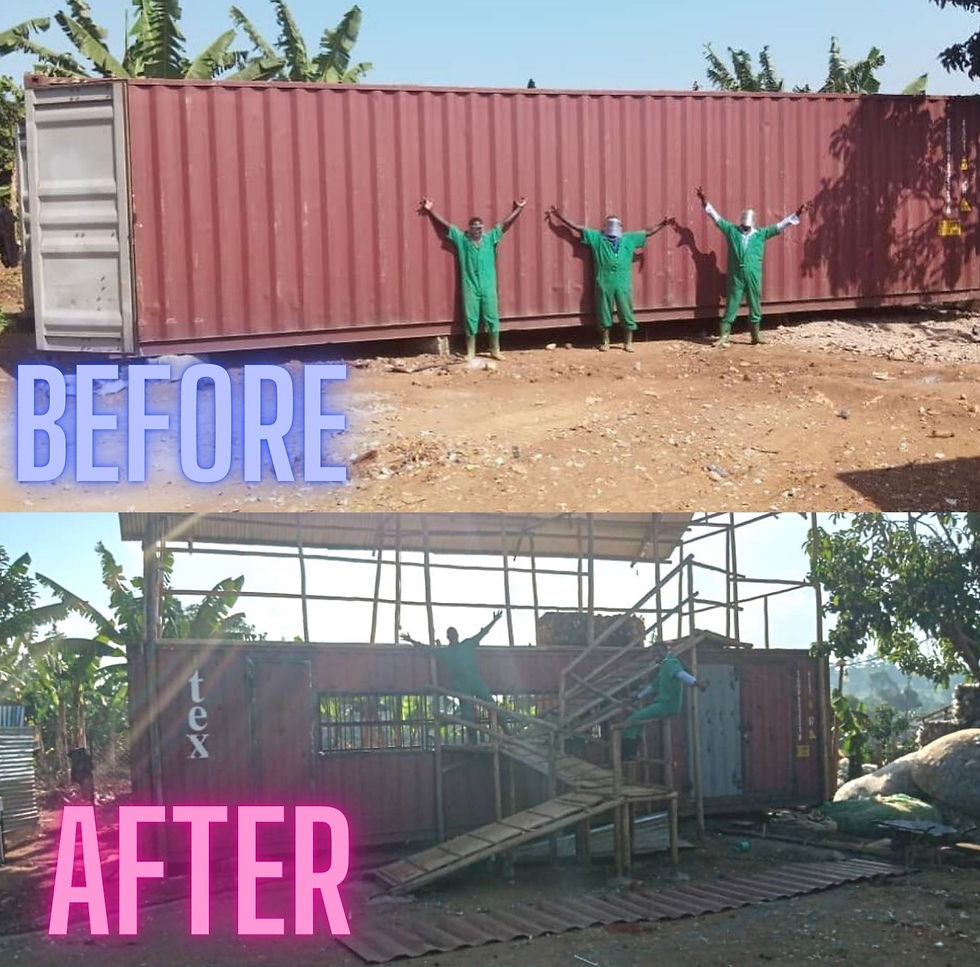
In one of our more ambitious idea, instead of building a new factory to house the machines, we purchased a 40ft second-hand shipping container that we converted instead!
We included ramps to the new structure to ensure it was accessible to our disabled team members. This was especially important as we focus on disability employment in Uganda and over 50% of the team are from the disabled community.
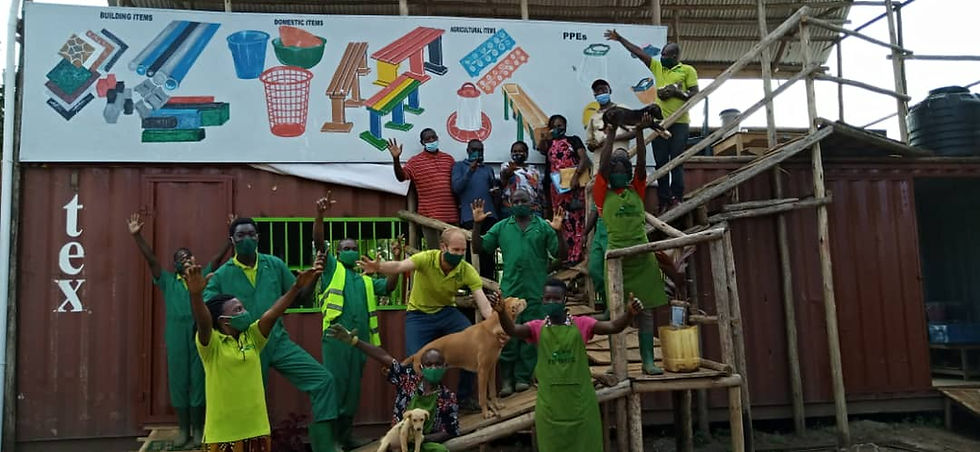
Furthermore, we hired a local artist to decorate the new structure, to create a nice environment for the team to work in.
We updated our marketing for the community...
We also got local artists to redesign the images on the walls of the grounds so the community can easily understand our model and how they can benefit from it. Namely, how we'll exchange their plastic waste for cash, and then recycle it!
We created an education hub on-site...
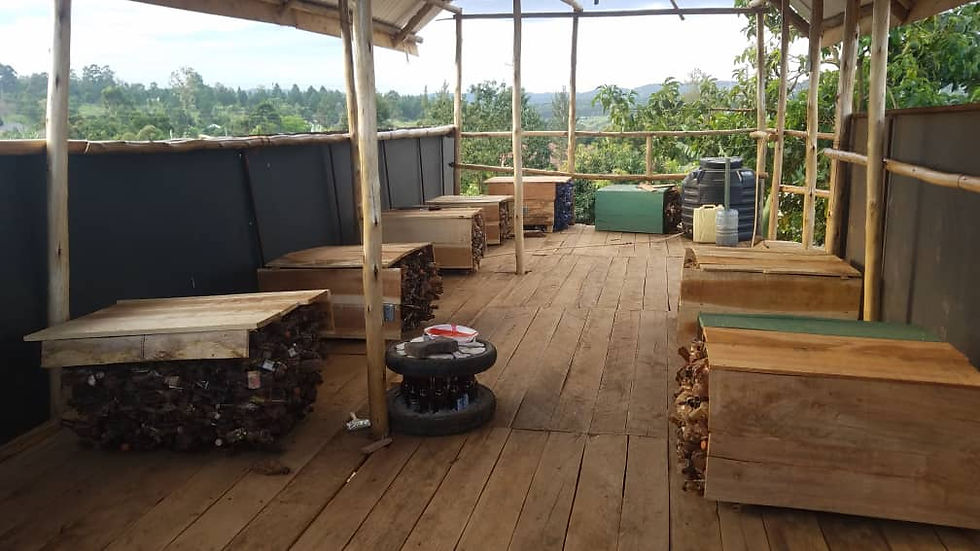
On the roof of our new factory structure, we created an education space where we can host school pupils when they visit our main site to learn about they too can protect the environment. This is apart of our Eco Clubs initiative, where we educate the next generation on how to look after the planet.
And the seats you can see photoed above - these were each made from recycled plastic... 1,300 bottles to be precise! :)
We created a method to wash plastic by harvesting rainwater...

A key part in the process of recycling plastic into new products is first washing it to ensure it's clean. Therefore, to save water, we've installed a drainage system throughout the site, which collects rainwater and stores it until needed, so we can clean the plastic in an environmentally-friendly way!
So after gradually building our collection network across the region over the last three years, it's been an exciting year converting the site to have the capacity to create Eco-Products from plastic waste, which has been the next key step in our journey to create a closed-loop system, which is independent of the international market.
Next, we plan to use the remainder of the year honing our skills in making Eco-Products, ready to sell on a larger scale next year. Simultaneously, we'll be extending our grounds further to create a second factory line, which will be able to produce the very bricks in our name!
So it won't be too long before we've got more photos to share with you showing how Eco Brixs HQ has developed even further - all with the mission of protecting Uganda's environment whilst creating jobs for the community! :)
Comentários